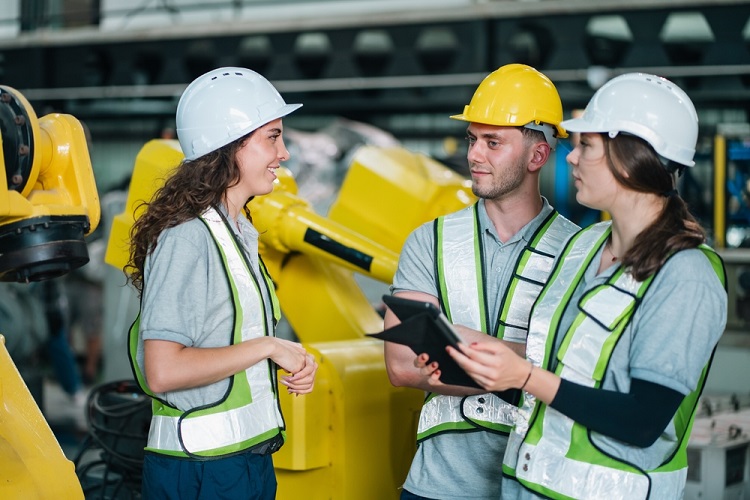
What U.S. Manufacturing Workers Are Looking For
For years, American policymakers have pushed to bring manufacturing jobs back to the U.S.—but there’s an important question that’s lingering: do Americans actually want those jobs? Despite efforts to reshore factories and restore industrial hubs, manufacturers are struggling to fill roles in what has become a tight labor market, suggesting this is less a job creation issue and more a matter of aligning with what today’s workforce actually wants.
Manufacturing Employment—Labor Shortage of 3.8 Million
According to the Manufacturing Institute and Deloitte, the manufacturing industry is expected to face a shortfall of 3.8 million workers by 2033, with about half of those positions not being filled. The workforce is aging rapidly: the average age of a manufacturing employee is 44, with 25% over age 55, and just 8% under 25. Young people aren’t entering the field, and older workers are retiring. But the issue isn’t a lack of jobs or skilled workers—it’s a lack of willing skilled candidates.
Modern-Day Manufacturing Workers
Today’s manufacturing workforce is more diverse, tech-aware, and value-driven than it was in decades past—but expectations are also significantly higher. Despite modernizations and advancements in the industry, many Americans still associate factory jobs with poor conditions—arduous labor, extreme temperatures, and rigid schedules, especially compared to tech or service jobs. Though rather outdated, these views seem to deter younger and more diverse talent from even considering the sector.
Jobs in the Manufacturing Sector
The demand for workers spans every level of the sector, from entry-level roles to specialized technical positions. The most in-demand positions include industrial mechanics, CNC programmers, maintenance technicians, and machine operators—roles that require both technical training and hands-on experience. Programs like FAME (Federation for Advanced Manufacturing Education), which offer earn-and-learn apprenticeships, are helping bridge the skills gap, but many employers still struggle to attract qualified talent fast enough, and even well-paying jobs are going unfilled.
In aviation manufacturing, for instance—which has been the subject of recent government reshoring efforts—companies report difficulty hiring for high-skill positions like turbine technicians and assembly engineers. While pay is obviously a huge motivator, it’s not just about wages for talent in manufacturing. Workers are looking at the whole employment package: culture, purpose, growth potential, and long-term stability. Without aligning with these values, employers risk losing out to industries that are moving with the times and doing more to meet workers where they are.
What Are Manufacturing Employees Looking For?

The 2025 Career Advancement in Manufacturing Report — conducted in partnership with Xometry, Thomas, and Women in Manufacturing — gave us a clearer picture of what workers want. Based on data ranges that include both early-career and late-career respondents across multiple U.S. regions, the report provides actionable insights into recruitment strategies, employee retention, and how to build a more inclusive and supportive workplace.
Encouragingly, 80% of respondents recommend careers in manufacturing, and 78% of women say they’ve seen significant progress for women in the industry over the past five years. However, it also highlights some ongoing workforce challenges. For instance, 79% of manufacturing companies report experiencing labor shortages, and 74% of women—compared to 49% of men—say they “fell into” manufacturing, suggesting gendered pathways into the field.
Here are some more insights from the report.
Skill Development and Job Growth
Workers—especially Generation Z and women—are actively looking for structured career development. They want training programs, mentorship, and clear paths to advancement, not dead-end jobs. Apprenticeships, leadership tracks, and on-the-job education are no longer nice bonuses—they’re expected.
Flexibility and Work-Life Balance
Rigid shifts are out, and flexible work arrangements — such as compressed workweeks, shift-swapping, hybrid working, and job-sharing — are becoming major priorities. These options are especially important for parents, caregivers, and those balancing multiple responsibilities. Companies that embrace flexibility have higher retention rates and a broader talent pool.
Safe, Comfortable, and Tech-Enabled Workplaces
Manufacturing roles can be physically demanding, but modernized facilities and ergonomic equipment can significantly improve the working experience. Workers want safe, clean, well-lit, and tech-enabled spaces with up-to-date machinery. Temperature-controlled environments and reliable equipment aren’t luxuries—they’re the baseline for physical well-being and labor productivity.
Diverse and Inclusive Culture
The data also confirms that an inclusive workplace is no longer optional. 87% of women and 56% of men in manufacturing believe diversity leads to better outcomes. Workers want to see DEI initiatives that go beyond lip service: real representation, allyship training, and proactive outreach to underrepresented groups.
Fair Pay and Respect
Competitive pay is essential, but it’s not the only thing workers are looking for. They want to feel valued, respected, and treated as professionals. Toxic cultures, poor communication, and disrespect from supervisors are dealbreakers. Today’s talent expects transparency, consistency, and a culture where everyone has a voice, regardless of background or title.
Community Connections and Career On-Ramps
Partnerships with local colleges, nonprofits, and workforce development boards make manufacturing more accessible. Programs like FAME show how public–private models can provide real-world experience, mentorship, and job readiness, particularly for first-generation workers or career switchers.
Sustainability and Social Impact
Sustainability isn’t just a fad—it’s a core value for younger workers. Over 40% of Gen Z employees say they prefer to work for companies with visible, meaningful environmental commitments across their supply chains. Manufacturers that adopt green practices and communicate them clearly will have a recruiting edge, especially among values-driven younger workers.
Positive Employer Brand and Employee Voice
A strong employer brand matters. Today’s workforce looks at employee testimonials, online reviews, and social media presence before applying, often turning to platforms like Glassdoor and Indeed for honest insights. They also expect internal listening channels—pulse surveys, suggestion boxes, open forums—that make them feel heard and included in decision-making. Transparency and two-way communication build loyalty.
U.S. Manufacturing Jobs and Workforce—Summary
U.S. manufacturing has deep roots in the Industrial Revolution, but reached phenomenal heights and global prominence during World War II. Since then, it has grown into a billion-dollar industry recognized worldwide. However, it’s going through significant changes.
While manufacturing employment experienced steady but cyclical growth in recent decades, employment declines in other industries and subsectors—such as the apparel and textile industries—contrast with increased demand in transportation equipment, fabricated metal products, food manufacturing, and computer and electrical products.
Despite a relatively low national unemployment rate, the Bureau of Labor Statistics reports hundreds of thousands of open manufacturing positions today. Deloitte estimates a shortfall of 3.8 million by 2033, half of which may go unfilled unless the American manufacturing sector adapts to modern workforce expectations.
Many manufacturers cite the talent gap and the struggle of retaining talent as a primary business challenge, with a particular focus on digital skills and attracting workers with at least some college education or a four-year college degree. Initiatives like the Science Act and partnerships with education affiliates aim to address these gaps, but further widening between job openings and available candidates persists.
As executive directors at national associations warn (and economic analysis suggests), the industry’s future depends on adapting to these realities and creating hundreds of thousands of new jobs that appeal to modern workers.
Image credit: Chokniti-Studio/Shutterstock